Instruction about Composite Material
1 Definition
Over two kinds of material are composed chemically and physically. These have a different phases with former material which show better ability. GFRP were formed by reinforcement, and matrix the year of 1940. Furthermore 1960 CFRP were invented to be used in various ways instead of metal or ceramic structure for vessel, aircraft etc .
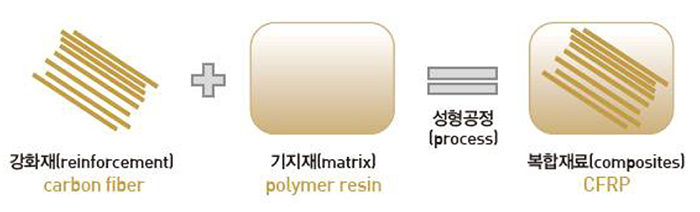
2 Feature of Composite Material
- 1) Low density
- 2) High specific strength
- - For the low density, specific strength and inelastic factor is higher
- 3) High decrement
- - High decrement of matrix
- - For the high specific strength original frequency is higher and absorb outer vibration
- 4) Absorption of external vibrations
- 5) Low coefficient expansion
- - Direction toward fabric, it has low coefficient expansion
- - It can be used in spacecraft extreme low and high temperature
- 6) Anisotropy
- - Direction toward fabric strength and rigidity is higher
- 7) Brittle fracture
- - Generally it is not return yield point before it is broken.
- 8) Resistance against fatigue and corrosion are high
- 9) Low slip coefficient and resistance against abrasion
3 Feature by sorts of reinforcements.
- 1) 1) Sorts of reinforcements
- - Long fabric, Particle, Flake, Whisker, None flammable fabric, Filament, Sheet
- 2) Fibrous composite
- - Glass, Boron, Carbon. Biological, Aramid, Ceramic, Metal
4 Feature by sorts of matrix
- 1) Sorts of matrix
- - Polymer, Metal, Ceramic
- 2) Polymer matrix composite
- - Thermoset polymer
- · Epoxy : Used for spacecraft
- · Polyester/Vinylester: Automobile, vessels, electrical
- · Phenolic : BMC(Bulk Molding Compound) production
- - Thermoplastic polymer
- · Nylon, Thermoplastic polyester, Polycarbonate, Ployvenyl PPS, PE
- - Metal matrix composite
- · Al alloy, Ti alloy, Mg alloy, Stainless
- - Ceramic matrix composite
- · Al2O3, Si3N4, SiC, Carbon
- - Thermoset polymer
- 3) Work of matrix
- - Transfer stress and protection fabric.
5 Composite Material Molding
- 1) Filament winding
Impregnation resin into FRP(Fiber reinforced plastics) filament and Winding fabrics on surface of rotating Mandrel. It is used for pipe or circle shape parts.
- - Feature
- · High strength for infusion of fiber continually
- · Pressure vessel, Pipe, and Angle winding is possible.
- - Feature
- 2) Vacuum Bag Molding
Laying up Prepreg on Mold and hardening in high temperature and high pressure in vacuum system.
- - Feature
- · High pressure in vacuum help to combine between plys tightly The best production condition.
- · Physical properties are good, trustworthy in quality production
- · Longer procedure and high cost.
- · Complicated production (Vacuum bag production and hardening in Autoclave)
- - Feature
- 3) RTM(Resin Transfer Molding)
It is similar to Infusion but upper and bottom face of part, a mold is used.
- - Install dry fabric on mold cavity, and insert resin to the part.
- - VARTM(Vacuum assisted RTM) : In vacuum system liquid resin is inserted. It can remove void which can immerge in the method of RTM
- - Feature
- · Production time is short, so it is useful for mass production.
- 4) Compression Molding
Genearal production process for polymer composite. Inserting composite into a mold produce part with high pressure and temperature by auto press or manual.
Moldingtransfer is developed after automated pressured - 5) Hot Press
Place prepreg on a Hot press, produce a part with high temperature and pressure.
Flat parts are easy to produce but curved part can be produced by mold. - 6) Infusion Molding
Place dry fabric on a mold after laying up inserting resin with vacuum bag.
For large size of composite part it is used widely. - 7) SMC (Sheet Molding Compound)
On Resin compound, which are made in liquid matrix mixture with low shrink, filler, hardener, thickener, and pigment, fabric reinforcement is impregnated.
Thermosetting medium material a shape of sheet.
It is good for automation and short a time for molding. So it is used for mass production.
Architectural materials(water tank), and bath room equipment(Basin, water prove panel, ceiling, ...) in various ways. - 8) LFT (long Fiber Thermoplastic) 공법
LFT is a composite polymer material, on thermoplastic polymer reinforced long fiber. Long Fiber Reinforced Thermoplastics.
By a Pultrusion Process impregnates thermoplastic into filament, in various way, these are able to be applied to injection mold which can produce a shape of pellet.
Materials for LFT is Short Fiber, compared with reinforced polymer material, a length of fiber is longer it is able to show better physical properties.
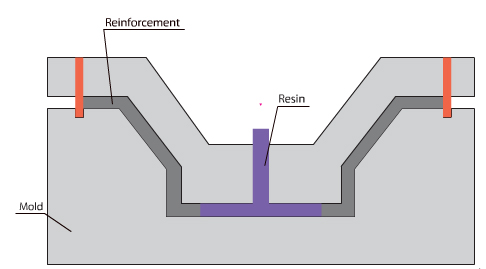